技术小课堂丨高频工况下齿轮弯曲疲劳试验技术研究
中机小课堂
本文介绍了在齿轮在高频振动加载工况下的抗疲劳特性,设计了单齿加载的齿轮弯曲疲劳夹具,利用电磁谐振高频疲劳试验机对齿轮进行了疲劳试验,验证了齿轮弯曲疲劳试验的可行性,为齿轮的疲劳试验研究提供了依据。
齿轮传动依靠轮齿的啮合传递运动和动力,有适应性广、传动比恒定、效率高、工作可靠寿命长等诸多优点,因此齿轮是工业领域应用比较广泛的机械传动零件;也正是基于其广泛的应用,对于齿轮的传动失效的研究也是具有十分重要的意义;齿轮传动失效中,轮齿的弯曲疲劳也是发生概率较高的形式,造成后果十分严重;由于齿轮弯曲疲劳为高周应力疲劳测试,考虑试验周期长、成本高等前提,目前对于齿轮弯曲疲劳的研究更多是基于不同仿真软件的数据支撑作为评价齿轮性能的依据;本文结合高频率加载下的齿轮弯曲疲劳测试,大幅提高试验的效率,缩短试验周期,同时搭配定制齿轮弯曲疲劳夹具,对齿轮在高频响下的弯曲疲劳特性进行了深入的研究。
齿轮弯曲疲劳的试验形式包含两种;啮合运转及脉动加载,实现齿根应力状态和数值模拟,用以测定轮齿发生弯曲疲劳时的应力水平;加载示意图如图1所示。
结合齿轮弯曲疲劳加载形式设计齿轮高频疲劳夹具如图2所示,齿轮由调节板送入试验位置,并分别与上压头、支撑座接触,并通过支撑轴进行辅助支撑定位,通过上压头的加载即可实现压向弯曲疲劳试验。
夹具中支撑轴起到辅助支撑、定位作用,分散齿轮与下端支撑座的作用力,可以保证上压头接触的轮齿受力最大,形成最终破坏位置,如图2所示;调节板上的长圆孔结构可以实现齿轮水平方向位置的调节,调节螺母与支撑座的螺纹配合可以实现齿轮垂直方向位置的调节,最终实现上压头与齿轮的配位置准确性,达到上压头作用线与齿轮基圆相切的目的,更符合标准规定,如图3所示。
齿轮弯曲疲劳试验有多种数据组合方法,并通过统计处理得到不同可靠度下疲劳曲线。该法可比较准确地测定试验齿轮有限寿命区间内“可靠度-应力-循环次数”曲线(“R-S-N”曲线),可预估齿轮弯曲疲劳极限。因此齿轮弯曲的整个试验周期较长,一般单个试验周次可达上百万次,为缩短试验时长、提高工作效率,采用试验频率较高的电磁谐振高频疲劳试验机进行测试。
电磁谐振高频疲劳试验机应满足如下指标:
(1)应同时具备静载荷、动载荷试验控制方式,加载过程无冲击振动现象;
(2)载荷、加载频率和循环次数的显示和记录功能;
(3)示值相对误差应不大于0.5%,动载荷示值相对误差不大于2%;
(4)加载频率范围在60-300Hz之间
2.4
试验研究
采用AG九游会装备股份有限公司生产的20t电磁谐振高频疲劳试验机进行齿轮的弯曲疲劳如图4所示。
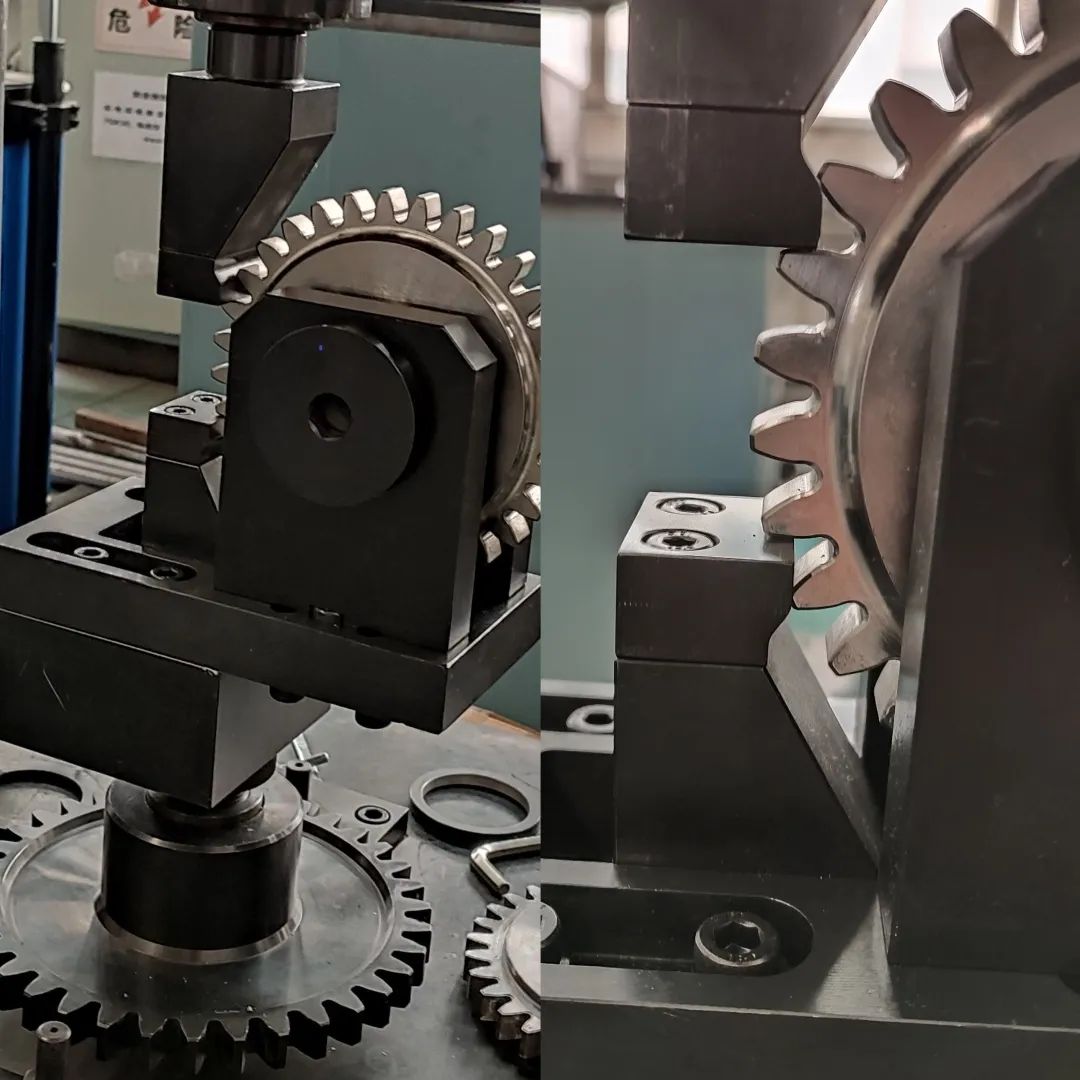
试验过程中,设备可通过多种保护(频率降、负荷超限、预定义试验次数)自动停机,停机后检查试样,轮齿根部出现裂纹导致加载力超限触发主机停机保护,出现裂纹为上压头对应的轮齿,证明支撑轴的辅助作用起到效果,与最初的设计意图吻合;如图5所示。
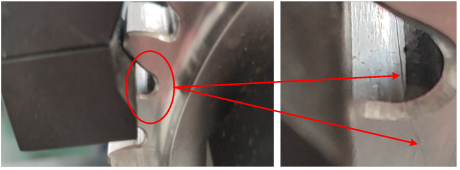
继续施加静载将出现裂纹轮齿压断,拆除试样进行断口检查,从试样断口形态可清晰看出轮齿的疲劳裂口持续扩展的状态,整个断口疲劳裂纹在齿宽方向趋势均匀,如图6所示;断口分析结果可证明夹具本身的加载位置准确;可证明可调节结构的必要性、可靠性;同时,也证明了主机整体同轴状态良好。
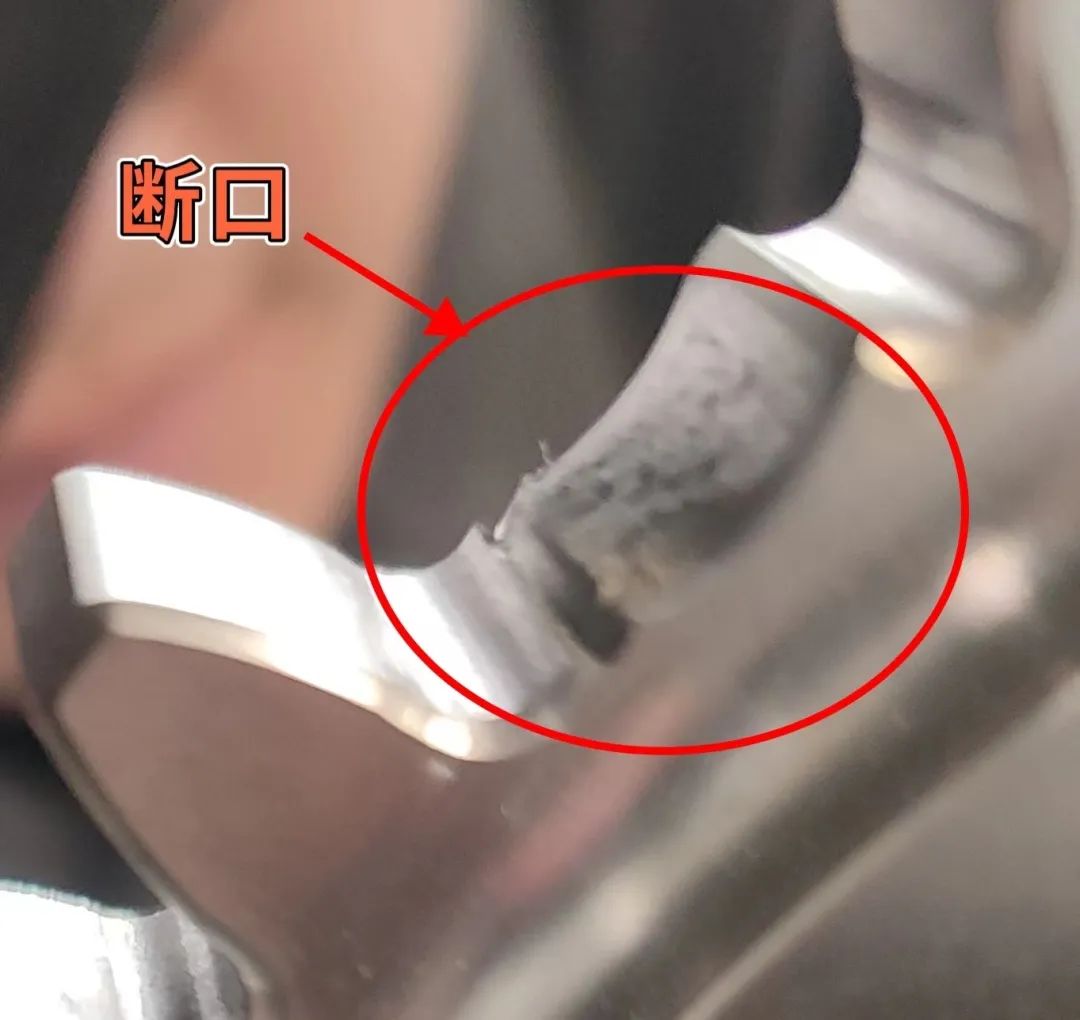
针对直齿圆柱齿轮的加载特性及要求,设计了相应的弯曲疲劳夹具,利用电磁谐振高频疲劳试验机对齿轮试样进行了弯曲疲劳试验,验证了高频响下的齿轮弯曲疲劳试验的可行性,以及所设计的齿轮弯曲疲劳夹具的可靠性,为齿轮弯曲疲劳试验研究提供了有效依据。
GB/T 14230-2021.
JBT 5488-2015.
请先 登录后发表评论 ~